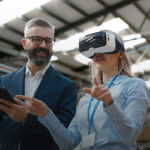
Inovações tecnológicas nas caldeiras: tendências e futuro
16 de dezembro de 2024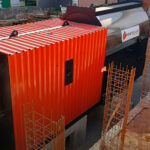
A relação entre eficiência energética e redução de custos operacionais nas caldeiras industriais
19 de dezembro de 2024Independentemente do setor ou indústria, é natural que os equipamentos, por mais importantes que sejam, tenham algum tipo de problema ao longo do tempo, não é mesmo? Não é diferente quando falamos das caldeiras industriais, que podem ter o seu funcionamento impacto em determinados cenários.
A boa notícia, porém, é que existem soluções para esses problemas também. Afinal, cada falha tem uma causa específica, um impacto direto na operação e uma solução que, quando implementada adequadamente, pode evitar transtornos maiores.
Continue a leitura para tirar todas as suas dúvidas sobre o assunto!
1. Acúmulo de depósitos e incrustações
Imagine um sistema onde a transferência de calor, essencial para a geração de vapor, é continuamente bloqueada por camadas de depósitos minerais. É exatamente isso que ocorre nas caldeiras quando a água utilizada contém altos níveis de sais dissolvidos.
Esses resíduos se acumulam nas superfícies internas, formando incrustações que comprometem a eficiência térmica e podem levar ao superaquecimento dos tubos.
Com o tempo, o equipamento passa a consumir mais combustível para compensar a perda de eficiência, aumentando os custos operacionais. Para resolver esse problema, o primeiro passo é tratar adequadamente a água antes que ela entre no sistema.
Para resolver, é preciso seguir processos como abrandamento e desmineralização, que removem os sais responsáveis pelo acúmulo de depósitos, enquanto sensores de monitoramento em tempo real garantem que a qualidade da água esteja sempre sob controle.
Além disso, limpeza dos tubos através da escovação manual para remover os resíduos já acumulados, e limpeza química em casos extremos, são soluções corretivas para tratamentos deficientes.
2. Corrosão interna
Em uma operação de caldeira, a presença de oxigênio e dióxido de carbono dissolvidos na água cria um ambiente perfeito para a corrosão.
Imagine tubos enfraquecidos por áreas corroídas, que, silenciosamente, comprometem a estrutura do equipamento até que um vazamento ou, em casos extremos, uma falha catastrófica aconteça.
Controlar a corrosão é essencial para manter a integridade do sistema. Soluções como desaeradores removem o oxigênio dissolvido antes que a água entre no circuito, enquanto produtos químicos específicos, como inibidores de corrosão, formam uma barreira protetora nas superfícies internas.
Além disso, o ajuste do pH da água mantém o ambiente menos corrosivo, preservando os materiais expostos. Em caldeiras de alto desempenho, aplicar revestimentos anticorrosivos também é uma prática recomendada, garantindo maior proteção contra os efeitos de longo prazo.
3. Falhas nos queimadores
Um queimador funcionando de forma inadequada é como um coração que bate fora de ritmo, prejudicando todo o sistema. Quando os bicos injetores estão obstruídos ou mal calibrados, a combustão se torna irregular, reduzindo a eficiência energética e aumentando as emissões de poluentes.
Resolver problemas nos queimadores exige um olhar atento e intervenções regulares. Primeiramente, a limpeza das peças remove resíduos que poderiam obstruir o fluxo de combustível.
A calibração periódica ajusta o sistema para garantir uma queima uniforme e eficiente, fazendo com que a mistura ar x combustível esteja sempre dentro dos parâmetros setados.
Em casos de desgaste excessivo, substituir componentes como bicos e válvulas é essencial para restaurar a funcionalidade do queimador.
Com essas práticas, é possível assegurar que a combustão esteja alinhada às necessidades da operação, reduzindo custos e impactos ambientais.
4. Vazamentos em tubos e juntas
Imagine um vazamento pequeno, quase imperceptível, em uma junta da caldeira. Com o tempo, esse problema aparentemente inofensivo pode evoluir para falhas críticas, aumentando os riscos operacionais e gerando prejuízos significativos.
Afinal, vazamentos frequentemente resultam de soldas mal executadas, materiais de baixa qualidade ou corrosão.
Para evitar que pequenos vazamentos se transformem em grandes problemas, inspeções regulares devem ser realizadas. Testes de pressão ajudam a identificar pontos de fraqueza no sistema antes que eles resultem em falhas visíveis.
Quando detectados, reparos devem ser feitos imediatamente, com soldas de alta precisão e, quando necessário, substituição dos materiais comprometidos. Além disso, o uso de materiais resistentes à corrosão nas juntas e tubos garante maior durabilidade e segurança ao sistema.
5. Formação de espuma e arraste
Em algumas operações, o vapor gerado pela caldeira industrial pode conter partículas sólidas, resultado da formação de espuma causada por água com alta concentração de sólidos dissolvidos.
Essa contaminação, afeta diretamente a qualidade do vapor, comprometendo processos produtivos e danificando os equipamentos que utilizam esse vapor.
Controlar a concentração de sólidos dissolvidos na água exige uma abordagem cuidadosa. Monitorar os ciclos de concentração do sistema ajuda a manter os níveis de sólidos dissolvidos dentro do limite ideal. Além disso, a utilização de produtos químicos antiespumantes reduz a formação de espuma.
Para maior controle, sistemas de purga automáticos podem ser instalados, removendo periodicamente a água com alta concentração de sólidos. Essas medidas garantem que o vapor produzido seja limpo e de alta qualidade, evitando danos a longo prazo.
6. Perda de eficiência térmica
Caldeiras são projetadas para converter energia térmica em vapor de maneira eficiente, mas essa eficiência pode ser severamente comprometida por falhas no isolamento, depósitos acumulados nos tubos ou trocadores de calor obsoletos.
Com isso, a operação da caldeira demanda mais combustível para produzir a mesma quantidade de vapor, aumentando os custos.
Manter a eficiência térmica requer atenção constante. Garantir que o isolamento esteja em perfeitas condições é o primeiro passo para evitar perdas de calor.
Além disso, a limpeza regular das superfícies internas remove depósitos que prejudicam a transferência de calor. Em casos onde os trocadores de calor já não atendem às exigências operacionais, a substituição por modelos mais modernos e eficientes pode trazer ganhos significativos.
7. Defeitos no sistema de controle
Um sistema de controle confiável é o cérebro que mantém uma caldeira funcionando dentro dos parâmetros ideais. Quando sensores, controladores, transmissores, pressostatos, manômetros ou softwares apresentam falhas, a operação fica sujeita a erros que podem levar a interrupções e riscos de segurança.
Garantir o bom funcionamento do sistema de controle começa com verificações regulares e calibração dos instrumentos de medição. Componentes eletrônicos devem ser inspecionados e substituídos assim que apresentarem sinais de desgaste.
Manter o software atualizado reduz vulnerabilidades e melhora a funcionalidade geral do sistema. Além disso, implementar redundância em sistemas críticos, como backups para sensores e controladores, assegura a continuidade da operação mesmo em caso de falhas inesperadas.
8. Falhas mecânicas em válvulas e bombas
Válvulas que não selam corretamente ou bombas que não funcionam como deveriam, representam desafios comuns em caldeiras industriais. Esses problemas geralmente são causados por desgaste mecânico, lubrificação inadequada ou peças de baixa qualidade.
Manter as válvulas e bombas em perfeito estado requer um plano de manutenção detalhado. A lubrificação regular é essencial para reduzir o atrito e prolongar a vida útil dos componentes. Substituir peças desgastadas antes que falhem completamente evita paradas não planejadas.
Além disso, o uso de tecnologias de monitoramento preditivo, como análise de vibração, permite identificar problemas em estágios iniciais, reduzindo o risco de falhas graves. Com essas ações, é possível manter o fluxo de água e vapor constante, garantindo a eficiência operacional.
Problemas em caldeiras industriais são inevitáveis, mas, com um diagnóstico preciso e a implementação de soluções técnicas adequadas, seus impactos podem ser minimizados.
Cada desafio exige uma abordagem específica, mas práticas como manutenção regular, uso de tecnologias de monitoramento e treinamento da equipe são indispensáveis para manter a confiabilidade do equipamento.
Além disso, contar com um equipamento confiável e de qualidade é fundamental, exatamente o que está disponível na Heat Boiler. Entre em contato com a nossa equipe comercial e descubra como as nossas soluções podem ajudar!