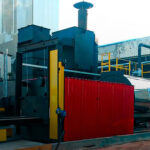
Estratégias para otimizar a operação de caldeiras em ambientes industriais
20 de dezembro de 2024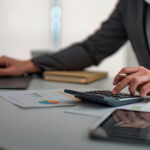
Como otimizar custos operacionais utilizando sistemas de cogeração
9 de janeiro de 2025A eficiência das usinas industriais está diretamente relacionada ao desempenho das caldeiras, componentes essenciais para gerar energia térmica ou elétrica. Mas como esses equipamentos conseguem impactar nas operações de uma planta?
A modernização, manutenção e o uso estratégico desses equipamentos têm demonstrado resultados expressivos em setores como geração de energia, petroquímica e alimentos.
O que acha, então, de conhecer alguns estudos de caso que ilustram como a eficiência pode ser melhorada por meio de melhorias específicas em caldeiras industriais? Continue a leitura e confira!
Qual é o papel das caldeiras na eficiência industrial?
Antes de mais nada, porém, é preciso entender que as caldeiras industriais têm um papel fundamental na conversão de energia, sendo responsáveis por fornecer o vapor ou calor necessário para diversas operações.
No entanto, problemas como perdas térmicas, baixa eficiência de combustão e acúmulo de resíduos podem comprometer sua performance. Para enfrentar esses desafios, muitas usinas têm investido em tecnologias avançadas e estratégias de otimização.
Mas alguns estudos recentes mostram que pequenas melhorias em caldeiras podem resultar em aumentos relevantes de eficiência, contribuindo para a redução de custos operacionais e emissões de carbono. Que tal conhecer mais sobre eles?
Case 1: otimização térmica em uma usina de açúcar e álcool
Uma usina do setor sucroalcooleiro no Brasil implementou um programa de modernização de suas caldeiras aquatubulares. O objetivo era reduzir perdas térmicas e melhorar o rendimento energético.
A usina enfrentava baixa eficiência devido a trocadores de calor desgastados e a sistemas de controle ultrapassados, que dificultavam a regulagem precisa da combustão. Além disso, as altas temperaturas nos gases de escape indicavam perdas energéticas que prejudicam a performance.
O processo de melhoria começou com a substituição de trocadores de calor por modelos mais eficientes, com tecnologia de recuperação de calor residual. Ao mesmo tempo, a implementação de sistemas automatizados de controle de combustão baseados em sensores de oxigênio e dióxido de carbono ajudou.
Outro ponto importante foi o isolamento térmico reforçado nas tubulações para minimizar perdas por condução. Com essas mudanças, a usina conseguiu tornar sua operação mais eficiente, reduzindo custos operacionais sem abrir mão do alto nível de produtividade.
Case 2: redução de consumo em uma usina termoelétrica
Uma termoelétrica localizada no Rio de Janeiro enfrentava um problema comum para muitas dessas usinas: dificuldades com o alto consumo de combustível em suas caldeiras a biomassa. A eficiência geral estava comprometida, levando a custos elevados e desempenho instável.
As análises indicaram que o problema principal era a queima incompleta da biomassa devido a uma distribuição irregular de ar no sistema de combustão. O acúmulo de escórias também contribuía para a redução da transferência de calor.
As intervenções começaram com a instalação de uma grelha específica e eficiente com divisórias estratégicas para a distribuição do ar de combustão. Ao mesmo tempo, a realização de manutenções preditivas para monitorar continuamente as condições operacionais ajudaram a promover um maior controle para os gestores.
O que fazer para melhorar a eficiência das caldeiras industriais?
Os casos mencionados destacam que, embora as abordagens possam variar, existem práticas comuns que contribuem para melhorias expressivas:
- Manutenção preditiva e preventiva: inspeções regulares e a substituição de componentes desgastados são essenciais para evitar paradas inesperadas e garantir a eficiência contínua;
- Automação e controle avançado: sistemas modernos, equipados com sensores de alta precisão, permitem ajustes dinâmicos que otimizam o consumo de combustível e a geração de calor;
- Adoção de tecnologias de recuperação de calor: equipamentos como economizadores e preaquecedores de ar ajudam a reaproveitar energia que seria desperdiçada.
- Capacitação da equipe: operadores bem treinados estão mais preparados para identificar problemas e ajustar as operações conforme necessário;
- Monitoramento constante: ferramentas de análise de dados em tempo real fornecem parâmetros valiosossobre a performance das caldeiras, permitindo intervenções rápidas e eficazes.
No final das contas, os estudos de caso evidenciam que a melhoria da eficiência em usinas com caldeiras industriais não depende apenas de investimentos em novos equipamentos.
Muitas vezes, ajustes relativamente simples, combinados com estratégias de manutenção e monitoramento, podem gerar ganhos substanciais. E o mais importante é entender que os resultados alcançados vão muito além da redução de custos.
Afinal, eles incluem maior estabilidade operacional, redução de impactos ambientais e aumento da confiabilidade dos sistemas, aspectos cruciais em um cenário de crescente demanda por eficiência energética e sustentabilidade.
Melhorar a eficiência em usinas com caldeiras industriais exige uma abordagem integrada, que combine inovação tecnológica, boas práticas operacionais e uma visão estratégica de longo prazo.
Na prática, gestores e profissionais do setor devem continuar investindo em tecnologias, capacitação e estratégias de manutenção para garantir que as usinas operem no máximo de sua capacidade, sendo mais eficientes e sustentáveis.
Quer entender mais sobre como as caldeiras industriais podem ajudar a tornar a operação na sua usina mais eficiente? Entre em contato agora mesmo com nossa equipe comercial para descobrir mais sobre a Heat Boiler!